Albert Heijn: Retail planned with OptiFlow
Albert Heijn’s distribution network is extensive and complex, as it consists out of 1,100 Albert Heijn stores, 600 Gall & Gall shops, 530 Etos locations and seven home shop centers. By using route planning software OptiFlow, the retailer aims to take maximum advantage of the network density of all 2,237 affiliated stores. “This would not have been possible with our existing route planning software. Luckily with this flexible Cloud solution, we are able to take the most complex rules and restrictions of our network into account”, says Martijn Beerepoot, project manager distribution and transport.

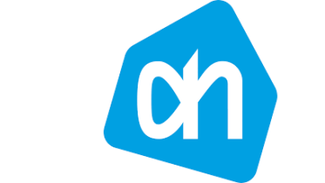
Continuously growing network
Planning routes for an extensive network is not an easy task. Moreover, this is becoming increasingly challenging since the retailer’s network is continuously expanding. For example, the collaboration between the BP petrol stations and Albert Heijn’s To Go shops. “Every location, small or large, has its specific characteristics. From time to time, we acquire existing stores such as Van Deen. This means that we continuously need to be able to respond and adapt to new situations”.
Network expansion requires flexible route planning software
According to Beerepoot, Albert Heijn’s growing retail distribution network primarily requires more flexible route planning software. “Despite the fact that our operations concern moving goods from one place to another, we demand quite a lot from the product. We supply a considerable amount of locations with their own characteristics, in multiple ways and in very specific time windows”. For example, the retailer supplies store A between 3 and 4 p.m. with processed foods, between 8 and 9 p.m. with fresh foods and somewhere in between with frozen foods. At the same time, local restrictions must be taken into account: at what times are you allowed into a town or city center, and with what type of truck can you reach the store? “If you have to enter the center of Amsterdam or Ghent, you cannot get there with the largest truck. You have no choice but to use a small box truck. These are all specifications that you have to take into account in your planning”.
Route planning software contributes to process control
“We deliver the planning to the carrier, who then assigns drivers to each route. Our department works on the basis of locations and therefore takes into account which vehicles are allowed to access which stores. Some locations for example, are supplied with emission-free vehicles. What Beerepoot also wants to emphasize is that the use of OptiFlow is a major step forward in process control. “Many transport departments still mainly rely on Excel. This naturally leads to a single point of failure within your organization because its use is still highly dependent on the knowledge in someone’s head. By choosing this new solution, we have one integrated planning application that is robust. Ideally, we would like as many activities as possible take place within this tool”.
The Results
Less pressure on the DCs
One of the goals Albert Heijn has set itself with the use of OptiFlow is smoothing out the peaks at DCs, so not all vehicles arrive and leave at the same time. Today, the planners try to accomplish this manually in the best way possible. “As a transport planner, you can manually move individual routes slightly forward or backward when peaks occur. This consequently results in less simultaneous departures per hour. In practice however, we notice that this is not the most optimal way of working.” Albert Heijn has now identified a next improvement for which they want to call on the expertise of PTV Logistics. The software will evenly distribute the departures while generating the plan, so planners no longer need to make this manual adjustment.
Continuous improvement in route planning
Albert Heijn strives for continuous improvement in their planning results. In addition to the fact that their plans are regularly adjusted, they are also compared to each other. Albert Heijn was one of the first Conundra customers (now part of PTV Logistics) to use the OptiFlow AI Technology to calculate with which parameters they could achieve the best results. With OptiFlow DOE (Design of Experiments) for example, a large number of relevant configuration combinations can be experimentally calculated, in an intelligent way, in order to determine which tiny adjustments positively impact the plan results. “Through comparison, we can steer towards the desired outcome”.
Responding to market problems
Continuous replanning and comparing leads to insight, says Beerepoot. “Before, your job was done as soon as you could lay down a plan. Now you have the time to evaluate alternative plans against each other”. Beerepoot indicates that Albert Heijn is now better able to respond to what the market demands. For example, taking driver shortages into account. “OptiFlow enables you to make a choice: Do I choose the cheapest plan? Do I choose the plan with the least number of kilometers and therefore also CO2 emissions? Or do I choose the plan with the least number of drivers, making their tasks as optimal as possible but maybe adding a few extra kilometers to the plan? My point is, you can really visualize what you want to achieve”.
Taking driver preferences into account
Aside from scheduling drivers in the most optimal way, it is just as important to keep drivers happy. One way to do so is by taking their preferences into account while planning. Beerepoot explains: “For example, drivers prefer their break to be scheduled for when they are at a DC, so they can eat at the canteen, not somewhere halfway a route along the highway. Consequently, we look closely at the structure of a route and set our drivers’ break settings in OptiFlow to match their preferences.”
In addition, they strive for high quality output. “It is essential that we achieve a plan of great quality, otherwise our drivers could decide to drive for someone else”, says Beerepoot. “If it is a half hour drive from a DC to a store, and you know the driver will be stuck in traffic, then you need to include this in the planning. With OptiFlow, we take traffic data into account which ensures that we can provide that quality”.
Close cooperation
Both during and after the roll-out of the route planning software OptiFlow, there has been good and close cooperation between the parties, according to Albert Heijn’s project manager distribution and transport. “PTV Logistics is a great and energetic partner with extensive knowledge. Above all, they speak our language”. He is also pleased with the adaptability of the software. “It is great that OptiFlow is continuously developing. New functionalities are added to the standard platform every two weeks. Sometimes, as a customer, we can even have an influence on what is developed. For example, one of the features in OptiFlow was developed through our input, which enables you to indicate how many minutes after the start of a driver shift, he/she can be scheduled a break. This prevents breaks from being scheduled too early on in the route.
New algorithms, more computing power
Making all these calculations on a large scale requires more computing power than before. Therefore, Albert Heijn is co-investing in the development of greatly improved algorithms that allow the use of more powerful servers. This makes planning even faster and cheaper. “In practice, this comes down to the use of super Cloud computers and very specific algorithms, that give us the same or even better plan results in much less time”. This investment is of great value to Albert Heijn since it means their network plan no longer takes 220 hours, but only a fraction of this time. Beerepoot continues, “Now we can make a new plan ten to fifteen times a year, instead of only three times a year. Eventually, we will have a new plan every week. This decreasing lead-time allows us to act more quickly, solving partial problems simultaneously and checking whether the KPIs are correct. This enables us to reduce the cost per order and increase our vehicles’ load factor”.